Necessity really is a mother. Especially for extruded aluminum builds.
Hey there slackers, hackers and makers. My name is Mark and I’ve spent a considerable portion of my life as a maker building with a wide variety of materials. I’ve built with wood, plastics, and metal – specifically in the form of extruded aluminum. I regularly searched for tools and jigs that would help me get the most out of this medium. And if you worked with extruded aluminum, I’m certain you searched too.
Considering the popularity of extruded aluminum in the maker space I figured there would be a good set of tools I could purchase or even make or print myself that would allow me to build with reasonable accuracy. Sadly, what I, and presumably you also, found was a plethora of 3D printable files, all different designs, all supporting different slot variations, useful for one or two different rail dimensions and never with a lot of consistency between them. I printed and used many (probably most) that I found. I’ve broken or lost many and reprinted. One thing remained consistent. I always had too many of these single-purpose prints scattered everywhere and would always end up searching for the right one or waiting on a reprint.
I was sick of this. It was after a recent build that I needed to reprint a tool and wasted about 30 minutes waiting for the print to finish only to realize I had printed the wrong one. Frustration sank it’s claws in like I was a trout and it was an Osprey. I needed a better solution. It was an absolute necessity. And as the saying goes, “Necessity is the mother of all invention.” So inventing a solution it is then.
If I knew then the headaches I’d put myself through, would I do it all over? Abso-tively. What emerged from my caffeine soaked, under-rested brain is the solution to end all my nightmares. Hopefully it can help you with yours also - at least the ones specific to building with extruded aluminum. This isn’t going to solve the issue with clowns. Sorry.
After spending a lot of time looking back on projects and identifying the key needs, I came up with a few things.
• Joining two rails together at their ends – think creating a cube frame with butt joints.
• Attaching one or more rails along the length of another rail – think shelving.
• Running hidden wiring through the center channel of a wide piece like a 2040 or 4040 rail.
With these primary needs identified, I spent some time reviewing the jigs and guides I used for these specific tasks. I still ended up with about seven of these 3D printed doohickeys that I would need to keep around all the time and a few more that I would need to keep in the “ready to print” queue for the rare occasion that I was working with anything other than 2020, 2040, or 4040.
The things I liked about the seven that I chose was that they were designed with bushings or sleeve bearings in mind and were small enough to handle and use with a regular drill. No need for a drill press was a big winner for me, even though I own a drill press. Many makers don’t.
The thing I hated most of all is there was a dingus for 2020, one for 2040, another for 2060, etc. There wasn’t one that worked for much more than one or two of those sizes.
There was also no consistency for the bushings. Some would only support Imperial / Standard size drill bits. Others would only support Metric. Considering the bore channels in the end of 20mm extruded aluminum is sized for M5 screws, it would make sense to just settle on bushings with a 5mm bore, wouldn’t it? I thought so too.
Here’s another kick to the head. Some were designed to work with T-slot rails and others designed for V-slot rails. The T-slot designs *could* work with V-slot rails but not vice versa. So I decided I needed to standardize on fitting T-slot rails and get V-slot support for free. Definitely not the lyrics to “Money for Nothing.”
Finally, many of the designs weren’t easy or safe to hold while using a drill. Only a few of them had enough meat available to use simple clamps. This would often put my delicate fingers a little too close to things that like to eat fingers.
And there we have it. The specific needs – end joints, mid-rail joints and holes for hidden wire runs. If I could build in end tapping with little fuss, even better. I needed to handle nearly all sizes of rail – 2020, 2040, 2060, 2080, 4040, etc. I needed a standard bushing size and T-slot support at a minimum. And I wanted this in as few pieces as possible. I didn’t want to have to print out a small army of guides only to have one or more go AWOL or MIA. Simple, right?
Parameters defined, I set to work. I ordered a variety of 20mm profile aluminum in various dimensions from the most common suppliers - OpenBuilds, 80/20, etc. I measured and doodled. I devoted a LOT of time to learning FreeCAD because I’m not paying for Fusion360 and TinkerCAD is too basic for what I needed. Plus I like a challenge and FreeCAD is anything if not challenging. I didn’t realize FreeCAD would make me want to grow my hair just so I could rip it out.
Anyway, there was a lot of CAD work. A lot of 3D prints. A lot of testing, re-measuring, rework in CAD. A lot of going back to the drawing board and rethinking. Most importantly, there was a LOT of swearing. Not the generic stuff either. This was that primo, creative, alliterative stuff. Things that would make George Carlin proud.
At the end of it all, what emerged was a thing of beauty, elegance and simplicity. It was extremely versatile despite it’s very basic design. It solved ALL of the problems I set out to solve and more I didn’t realize I needed solved. Best of all is that it is only 3 pieces and takes less than an hour to print on most 3D printers. But wait there’s more. Those three little pieces come together to form a single drill and tap guide solution that just might, but not really, save humanity. Kind of like Voltron, but different.
Held together by 14 magnets and protected by 14 bushings, this is the one drill and tap guide system to rule them all.
Without further ado, dear maker and reader, I proudly present to you the fruits of my migraines, the reaped grain of my sleepless nights and the sum total of all my cursing at CAD. …drumroll please…
The ExtrudAlign™ 2020: Drill and Tap Guide System for 20mm Profile Extruded Aluminum

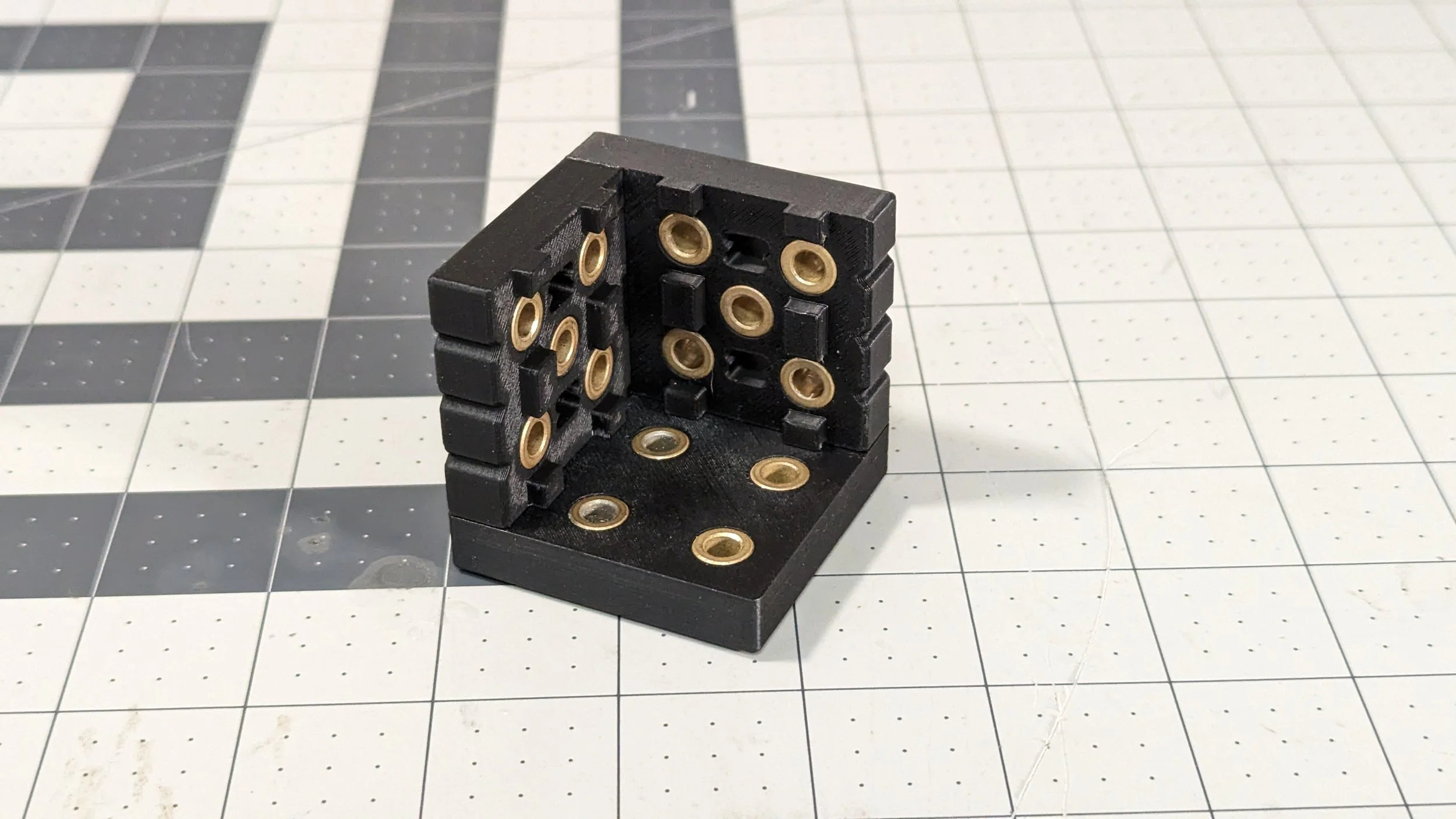


As you can see in the images, the three pieces snap together to form a half-cube. By design, the system supports 4040 right away and everything smaller. It offers plenty of surface area for safely holding to your work piece by hand or with clamps. It handles all of the drilling needs as well as tapping needs. It’s versatile enough to support 2060 and many other odd dimensions of extruded aluminum. The standard 5mm bore in the bushings is perfect for tapping the ends with a 5mm tap, drilling holes with a 5mm bit and is sized perfectly to allow for most center punch tools to do their thing in the event you need to mark the hole and drill smaller or larger than 5mm. There’s a number of marking and center alignment features for practically any need. And best of all, this one gizmo replaced about 12 or 13 different 3D prints I used to have.
You can purchase the STL and all the supporting materials from our shop to print it for yourself right now.
Or you can purchase a ready-to-use kit right now. We have a bunch already printed, quality-checked and ready out of the box just waiting for you.
Other Updates:
Our plans to source a limited run of the ExtrudAlign™ system milled from aluminum is sadly cost prohibitive at the moment. The current costs to make this a reality means that we would have to charge nearly three times more for the kit that we would like to. If we have sufficient interest in such a product and ExtrudAlign in general, we will consider resuming these plans.
If you really want us to make an aluminum version, let us know with the form button below.